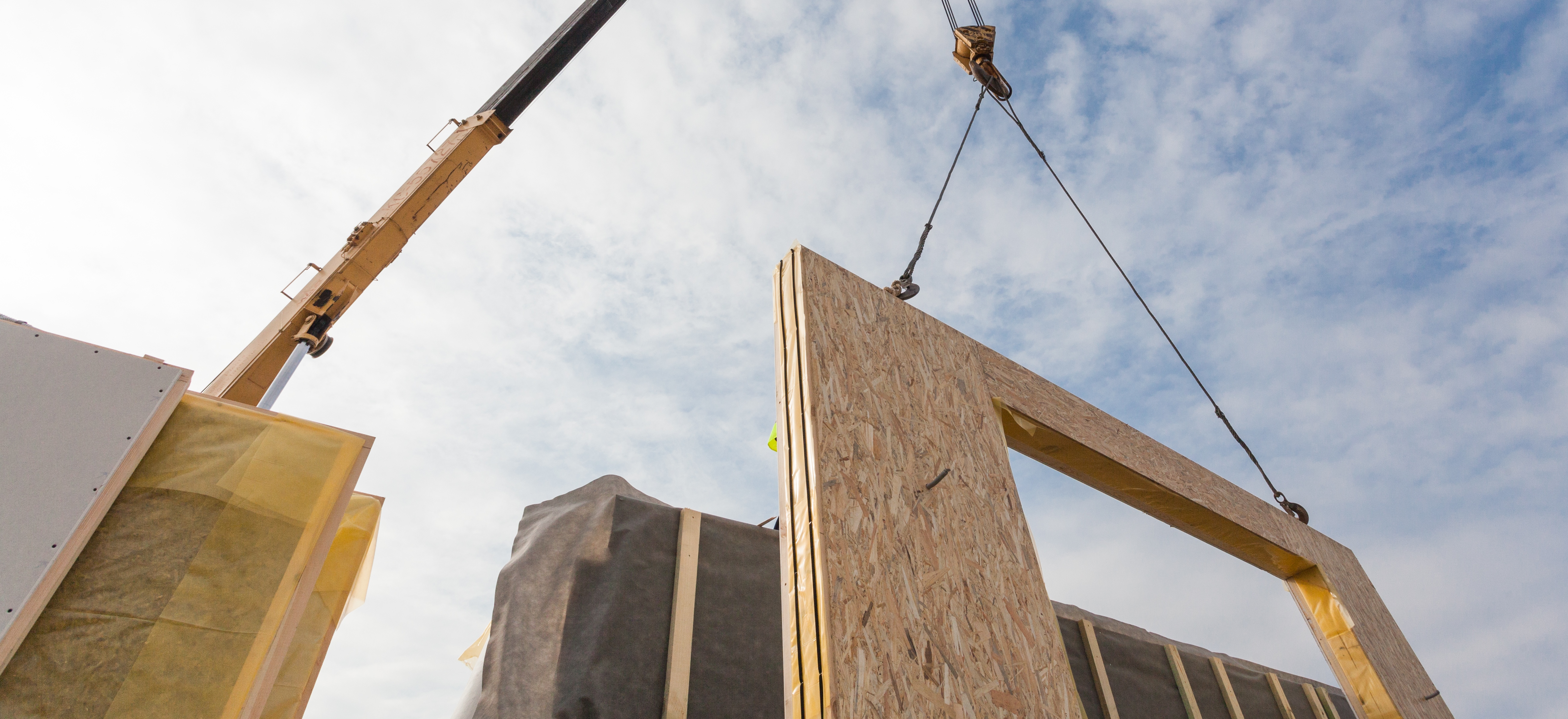
With more and more focus being placed on the way we as an industry can sustainably deliver buildings, MMC (Modern Methods of Construction) is a term that you cannot avoid. There is clear support to utilise these methods, but what impact does this route have on the role of Project Managers (PMs) and what they should be providing for their clients?
MMC is an all-encompassing term and can be any one of the seven categories, identified by the Ministry for Housing Communities and Local Government (MHCLG) MMC cross-industry working group (shown below). It is not just volumetric or pre-manufactured units but includes ways of improving existing working practices on site. The key is to focus on the word “methods”, rather than a preconceived idea of what type of MMC would be needed at the start of a project, unless this is already known by the client. This allows for a better conversation regarding what would be possible or appropriate for a project.
Currently, the main push for more MMC projects is by the Government, who are focused on providing more housing. However, these MMC definitions are now being carried over into the other industry sectors who can also benefit from these methods.
At concept stage the PM must ascertain the client’s high-level brief and core objectives to establish the likely project boundaries, targets and aspirations that need to be achieved. MMC can then be considered as a suitable solution that may help to achieve these objectives. The PM must have a sound understanding of the various options, opportunities and risks incorporating MMC would have, considering the earlier off-site pre-manufactured elements can be designed into the project, the greater the potential benefits. This will shape the direction of the project, in relation to the appointment of an appropriate design team, the project set-up, and in terms of cost and programme management and the procurement route. Whilst MMC elements can be introduced as the project progresses, there may be a risk that the pre-manufactured elements will lose their inherent benefits, such as the structural grids being incompatible or sub-optimal.
The construction industry is notoriously slow in taking up ‘new initiatives and practices’, often due to risks and costs involved, especially when there is limited data on the costs, programmes and the longevity of the various types of buildings that have used MMC as part of their construction. The drive to use MMC is, therefore, currently having more of an impact on those buildings that have more repetition where the benefits are more obvious, of which volume house building is a good example.
There are a multitude of considerations that will influence the way a project will move forward. Focusing on the four main issues of time, cost, quality and risk for the PM, the following are just some of the issues that will need to be considered:
- Programme – By utilising MMC and moving construction off-site, the overall time required on site can be significantly reduced. The reduction in programme and on-site activities can result in lower preliminary costs, a safer site and the building being occupied sooner. Despite the positives, the PM must be aware of potential delays and increased costs due to fluctuations in the delivery of the units. The PM must identify a clear programme with distinct milestones, including design development approvals and stage gates, that the client, design team and contractor are all invested in.
- Costs – The reliability of any initial cost estimates, especially with the current limited cost data available for bespoke projects, can shape the projects direction and will need to be reviewed closely with the Cost Consultants. The client will need to be aware of the potential for a higher spend earlier in the project. This front-loaded design and associated risks will mean that variations can have a more significant effect if the client or design team need to alter the designs. Control of costs due to the front-loading and potentially large subcontract orders will need to be carefully monitored and the client advised accordingly.
- Quality – It is especially important that the PM ensures that the Project Brief is quickly, comprehensively, and accurately prepared and agreed. This will include what is needed to be built, funded, and developed and if MMC elements are relevant and beneficial. If MMC elements are used, then the question whether the product is an accepted system with a warranty provider and/or has a Quality Assurance accreditation, or another recognised standard, will need to be raised. Any funder or insurance provider will need to accept the MMC elements in terms of construction materials, longevity of components and overall build, fire risks, saleability, cash flow profile (including advance payments) and many other factors. This could prevent certain levels of MMC being incorporated into a project potentially due to the lack of pertinent historical data or their own policies on risk.
- Risk – The risk profile will change with the method and processes used to complete a project. It is important for the PM to continually assess what the risks are with the project and understand any risks that will be introduced as the brief and designs change, such as the use of MMC. Health & Safety should be improved due to the controlled nature of a factory environment and the ability to control processes better. The reduced number of workers on site for a shorter period should also have a positive influence on this matter. Careful consideration of payment protection, in the form of bonds or guarantees needs to be considered during the procurement process and it may be advisable to seek surety of the modular or MMC supplier’s performance. Another consideration with MMC is the risk that a bespoke supplier has a problem for any reason which could have a serious impact on project continuity. There are several mechanisms for safeguarding against most of these effects in the form of warranties, bonds, and similar legal guarantees.
It is apparent that the role of a Project Manager is as important as ever when considering Modern Methods of Construction for your development. The complexities and unique situation for each project, client and location will impact on the project objectives and constraints. With new and different methods of construction that are being used in the industry, coupled with the current challenges the world is experiencing, Project Managers must be prepared to think differently to capture the best solutions and way forward for a project. Our Team are well versed with projects that have incorporated MMC, and if you require any further information on how GSSllp can assist with the Project Management of your project, please get in touch.